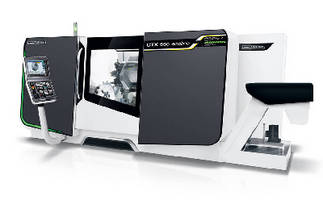
DMG MORI has introduced two new CNC turning centres, called CTX 450 ecoline and CTX 650 ecoline, the numbers indicating their chuck size in millimetres. They are the merged group's first jointly developed lathes.
Despite being entry-level models, they are of rigid design for dynamic, highly accurate metalcutting. Unusually in this class of machine, there is a choice of 3D control: SLIMline® with Operate 4.5 on Siemens 840D solutionline, Heidenhain CNC PILOT 640, or MAPPS IV on Mitsubishi.
Differentiating the machines from the competition are the FEM-optimised cast iron bed, large ballscrews, linear guideways for high rigidity and top positioning accuracy, and small footprints of 4.9 m² and 9.8 m² respectively.
CTX 450 ecoline is designed for highly accurate machining at spindle speeds up to 4,000 rpm, while the CTX 650 ecoline, with its water cooled motor, provides maximum torque of 2,000 Nm for heavy machining.
Respective figures for Z-axis travel are 600 mm and 1,150 mm and the bar capacity of these universal lathes is optionally up to 75 mm and 110 mm. The machines are equipped with an automatic tailstock for accurate turning and milling of shaft-type parts. The larger model can be fitted with a steady rest to allow shafts up to 350 mm in diameter to be machined. Linear scales for direct measurement of axis positions are an option to improve positioning accuracy from 0.02 mm down to 0.008 mm.
Both lathes have a servo driven tool turret with 12-stations, all of which can be live for carrying out complex prismatic machining in-cycle in conjunction with the C-axis. VDI 40 holders are used on the CTX 450 ecoline and VDI 50 holders on the CTX 650 ecoline. Tool change time is 0.4 seconds and rapid traverse in all axes is 30 m/min, contributing to short idle times.
Regenerative braking of the spindle and axis drives saves energy which can be used for accelerating the motors of other machines or fed back to the supply network. Linear guideways minimise friction and so also reduce energy consumption through the use of smaller motors. Furthermore, less lubricant usage mitigates environmental impact.
The CTX 450 ecoline can be fitted with the chip conveyor at the back rather than at the side, reducing the installation width of the machine by up to 35 per cent so that the production area can be used more efficiently and flexibly. |